Expanded Polystyrene Foamed Concrete Wall Panel Production Line
Lightweight EPS foam concrete wall panels manufacturing
Expanded Polystyrene Foamed Concrete Wall Panel Production Line
Lightweight EPS foam concrete wall panels manufacturing
In the EPS foamed concrete wall panel production line, cement acts as the binder, while EPS particles provide insulation. The primary raw materials include sand, fly ash, stone powder, and industrial waste residues. A physical foaming agent is used to aerate the mixture. During the foamed concrete wall panel production process, this foaming agent is diluted to a 1:40 ratio and transformed into a white paste foam via a foam generator. This foam is then pumped into a horizontal mixer and combined with the other raw materials. Our process incorporates advanced techniques from Germany's Luca Industries International, optimizing foamed concrete wall panel production lines to accommodate various capacity requirements.
We categorize the foam concrete wall panel production line into small, medium, and large categories, with a daily output of 100-1000m³ and power capacity of 200-600kW. We specialize in providing project planning solutions based on clients' equipment requirements and raw material properties.
-
Output: 500-10000m²/day
-
Number of operators: 6-15 person
-
Total area of plant: 5000-20000m²
- Examples
- Specifications
- Configurations
- Projects
Expanded polystyrene (EPS) foamed concrete wall panels, also known as self-insulating wall panels or homogeneous self-insulating wall panels. They are used for walls in cold and severe cold regions.
- Length: 2400mm, 2700mm, 3000mm
- Width: 600mm
- Thickness: 60mm, 90mm, 100mm, 120mm, 150mm, 200mm (customizable)
- Compressive strength: 3.0-7.5Mpa
- Panel density: 60-90kg/m²
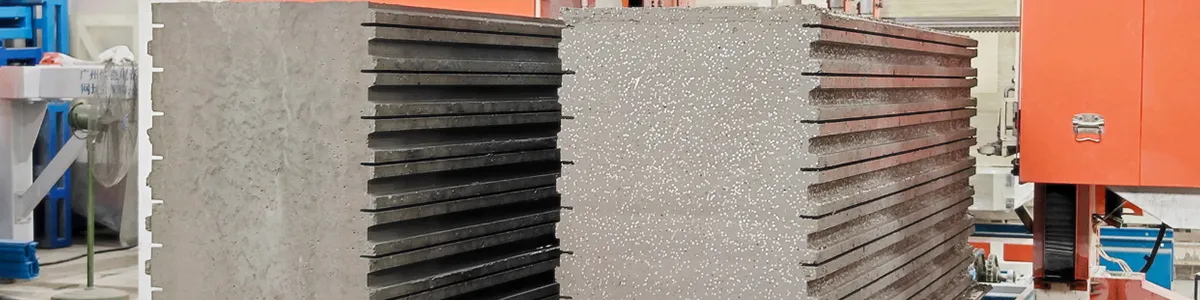
Required production space | Width:20-60m Length:80-200m Height:≥6m |
Curing area | 2000-8000m² |
Total power | 200-600kW |
Voltage | 380V |
Water consumption | 50-500ton/day (depending production output) |
Number of operators | 6-15 person |
Total area of plant | 5000-20000m² |
Output | 500-10000m²/day |
Temperature | Room temperature,≥ 0℃ (additional heating is required for below 0℃) |
Note: Water, electricity, and labor should be adjusted according to the production line output.
- High efficiency: featuring continuous online production and in-line cutting of the concrete cake, this system boosts production capacity. It also reduces the need for 3-5 workers per output, effectively lowering labor costs.
- Precision: high-precision, high-speed rotary band saw cutting of the concrete cake; with a cutting error of ≤1mm.
- Energy efficiency: the equipment has low power consumption, operates in segments, and has low energy usage, saving on electricity costs.
- Environmental friendliness: the equipment operates with low noise, uses water spray dust removal during cutting, and keeps the workshop dust-free.
- Flexibility: the production capacity can be freely chosen according to the type of mould; it allows for multi-type production with one machine serving multiple purposes.
- Reliability: authorized technology from Germany's Luca Industries; backed by an experienced technical team, ensuring worry-free after-sales service.
- Multi-functionality: can produce different types of wall panel products, such as foam concrete wall panels, EPS foam concrete wall panels, lightweight aggregate foam concrete wall panels, and aerated concrete wall panels.
To implement this EPS foamed concrete wall panel line, we have listed what you need to know for setting up the factory.